Причиной
разработки технических условий является использование современных
высокопроизводительных линий для розлива или упаковывания продуктов в
стеклянную тару. Так как банки и бутылки движутся с большой скоростью, любые
отклонения от размера или формы приводят к непопаданию в заданную позицию и, следовательно, к бою тары на конвейере, его загрязнению и остановке, к потере
продукта, т. е. к снижению производительности оборудования. Кроме того, продукты на этих линиях подаются в стеклянную тару под высоким давлением, что
может привести к ее разрушению.
Поэтому
некоторые ее виды должны отвечать повышенным требованиям (по сравнению с ГОСТом
10117-91) по геометрическим размерам и отклонениям формы, а также
гидростатическому давлению и остаточным напряжениям. Такие технические условия
чаще всего выдвигают потребители стеклянной тары. По действующим стандартам в
стеклянной таре допускается большое количество дефектов (газовых пузырей, инородных включений). Например, по ГОСТу 10117-91 — до 13 дефектов в
полулитровой бутылке. Обнаружив такое количество дефектов в бутылке марочного
коньяка, многие изготовители дорогой продукции стараются улучшить внешний вид
стеклянной тары, разрабатывая специальные технические условия.
Но
необходимо учитывать, что ужесточение требований приводит к повышению
себестоимости за счет увеличения количества отходов, затрат на систему усиления
контроля качества, более частой смены форм и т. д. Следовательно, растет и цена
готового продукта. При использовании такой стеклянной тары для упаковки дорогих
продуктов стоимость тары мало сказывается на конечной цене продукции наоборот, качество существенно влияет на оценку потребителя и на работу технологических
линий. Следует отметить, что многочисленные предложения иностранных поставщиков
высококачественной стеклянной тары, отвечающей требованиям российских ГОСТов
или техническим условиям, сдержат отечественного производителя от взвинчивания
цен.
3. Производство
стеклянной тары
Стеклянная
тара гигиенична, прозрачна, вместимость ее от 1 см3 до нескольких литров.
Различают узкогорлую стеклянную тару с внутренним диаметром горла до 30 мм и
широкогорлую — с внутренним диаметром горла более 30 мм.
Стекло
для тары должно быть хорошо проваренным, однородным, химически и термически стойким.
На внутренней поверхности изделий не допускаются пузыри и посечки, образующие
осколки и стеклянную пыль. Горло изделий не должно иметь заусенцев, выступающих
швов, острого края, посечек и т. д. Стекло для тары может быть бесцветным, необеспеченным (полубелым), окрашенным в темно-зеленый, оранжевый и другие
цвета. Стеклянная тара должна соответствовать установленной форме и допустимым
отклонениям по массе и размерам, а также удовлетворять требованиям действующих
ГОСТ и ТУ.
Контролю
качества стеклотары на заводах уделяется большое внимание. В зависимости от
вида тары и способа ее изготовления применяют соответствующие составы стекла, пример, для полубелой консервной тары состав стекла %: SiO2 —73, Al2O3 + Fe2O3
— 3—3,5; CaO+MgO —1 Na2O + K2O— 14,5; SO3 —0,3; F —0,5 (сверх 100%). Шихту для
полубелого и зеленого бутылочного стекла составляют из необогащенных песков, а
глинозем вводят с нефелиновым концентратом[6]
.
При
варке тарных стекол используют до 40% боя стекла, который следует промывать, дробить, сортировать. Для варки стекломассы применяют ванные проточные печи, в
отдельных случаях — горшковые печи. Размеры и конструкции стекловаренных печей
зависят от количества и цвета вырабатываемой стеклотары и способа ее выработки
(вручную, на полуавтоматах или автоматах).
В
зависимости от конструкции стеклоформующих машин, их производительности и
способа формования стекломасса должна иметь соответствующий состав.
При
выдувании стекло должно иметь достаточный интервал выработки (не быть
«коротким») и легко поддаваться обработке, для чего в стекле максимально
сокращается содержание СаО за счет увеличения количества SiO2 или R2O. Обычно
для изготовления сортовых изделий способом выдувания (из горшковых печей)
рекомендуется следующий состав стекла, %: SiO2—77—78; СаО—6—8; R2O—6—16,5.
Для
выработки прессованных изделий применяют составы с повышенным содержанием
щелочных оксидов. При производстве изделий механизированным способом составы
стекла должны обеспечивать большую скорость твердения в процессе формования, достаточную термическую стойкость и химическую устойчивость, что достигается
введением в состав стекла 1—2% Аl2О3 (за счет SiO2) и до 3% MgO (за счет СаО).
Способы
формования изделий. Прессование — наиболее древний способ формования
стеклоизделий. С усовершенствованием стекловаренных печей, в которых стали
получать менее вязкую стекломассу, оно было почти полностью вытеснено
выдуванием и применялось лишь для изготовления бус, пуговиц и других мелких
стеклянных предметов. Однако в первой половине XIX в. прессование вновь стало
одним из основных способов производства стеклоизделий.
Стеклоизделие
прессуют в форме, которая определяет внешнюю поверхность изделия, с керном
(пуансоном), создающим давление на стекломассу и оформляющим внутреннюю
поверхность. При ручном способе поверх формы устанавливают ограничительное
кольцо, которое предотвращает выход стекломассы из формы и оформляет края
изделия (рис. 1).
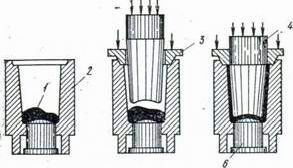
Рис.
1. Схема процесса прессования
1—
капля стекла; 2 — пресс-форма; 3 — ограничительное кол
4
— керн; 5 — изделие; 6 — поддон
Этот
способ прост, производителен, не требует от рабочего высокой квалификации и
поэтому дешев. Однако область его применения ограничена. Прежде всего
прессованные изделия должны иметь полость такой формы, которая позволила бы
пуансону выйти из нее, наружная же форма изделий может быть довольно сложной, иметь выступы и углубления, так как форма может раскрываться на две половинки.
Прессованием
не удается получать сосуды с тонкими или сильно вытянутой в вертикальном
направлении полостью, так как стекломасса слишком быстро охлаждается и теряет
текучесть. Прессованные изделия имеют дефекты в виде швов от стыков разъемных
частей форм, ребра и углы изделий получаются закругленными, поверхность кованой
и матовой. Поэтому прессованием; вырабатывают лишь дешевые массовые изделия (стаканы, пивные кружки, салатники, стеклоблоки).
Современный
ручной пресс — это массивный станок со столом для форм и стойками, на которых
смонтированы прессующие устройства. С помощью железного прута набирают
стекломассу и относят ее к прессу, здесь необходимую порцию отрезают над формой
специальными ножницами, далее форму закрывают формовым кольцом и ставят под
пуансон. Нажатием производят прессование с некоторой выдержкой пуансона в
форме, для того чтобы изделие приобрело достаточную жесткость. Затем пуансон
поднимают, форму выдвигают и снимают формовое кольцо. Изделие вынимают и
относят на отжиг. Далее все операции повторяются.
Коэффициент
полезного действия такого станка невелик, поэтому для повышения эффективности
прессования применяют сменные формы, что позволяет увеличить время их
охлаждения и производить одновременно несколько операций.
Формы
устанавливают на карусельном столе. При каждой остановке стола осуществляются
все параллельные рабочие операции. Пуансон охлаждают водой или сжатым воздухом.
Распределение стекла в форме зависит от температуры стекломассы, давления при
прессовании и равномерности остывания изделий в отдельных частях формы. Ручные
прессы вытесняются автоматическими или полуавтоматическими, которые создают
давление на керны при помощи сжатого воздуха. Сменная производительность
прессования вручную на рычажных пружинных прессах—400 крупных и 3,5 тыс. мелких
изделий, а на прессах-полуавтоматах — до 5 тыс. мелких изделий. Массовые
изделия диаметром до 250 мм, высотой до 150 мм и массой до 1,7 кг прессуют на
автоматах ПВМ или АПП. Суточная производительность прессов-автоматов при
выработке чайных стаканов — до 50 тыс. штук. Изделия прессуют металлическими
кернами в формах из легированных чугунов или сталей, отполированных до
зеркального блеска и покрытых смазками и защитными покрытиями.
Выдувание
— широко распространенный способ, дающий поверхность изделий хорошего качества.
При выдувании сначала получают в черновой форме заготовку (пульку, баночку), в
которую вдувают воздух при помощи трубки или специально й дутьевой головки с
полым керном. Выдувание производят в чистовой форме, в которой изделие
находится до затвердевания. После этого оно поступает на отжиг. Мелкие изделия
выдувают в форме сразу, без баночки. Выдуванием вырабатываются изделия самой разнообразной
конфигурации, разных размеров и с различной толщиной стенок.
Рис.
2. Схема выдувания изделия в форме
1 - дутьевая головка;
2 — керн; 3 — набор стекла; 4 — форма. Производительность ручного выдувания составляет
400—900 изделий в смену на бригаду из 6—10 человек.
Рекомендуем скачать другие рефераты по теме: торговля реферат, реферат на тему технология.
Предыдущая страница реферата |
1
2
3
4
5
6 |
Следующая страница реферата