Зола
|
0,6
|
0,2
|
0,4
|
0,6
|
0,3
|
0,1
|
изучения
ее состава. В электролитическом способе получения алюминия наиболее вредными
примесями являются железо, кремний, ванадий и сера. Первые три при электролизе
полностью переходят в металл, загрязняя его.
Вредное
влияние серы связано с ее окислением до сернистого ангидрида, который
взаимодействует с металлическими конструкциями электролизера. Образующаяся
окалина попадает в расплав, загрязняя алюминий железом. Кроме того, сера
накапливается в растворах газоочистки (при «мокром» способе очистки газов) и
требуется дополнительный расход содового раствора для вывода сульфатов из
процесса.
Известно, что натрий является катализатором реакции горения углерода. Большое содержание
данного металла приводит к повышенному расходу анодов, что увеличивает
себестоимость алюминия. Поэтому содержание натрия в коксе также лимитируется.
Отмечается сравнительно высокое содержание натрия в смеси коксов с ИркАЗа и в
коксе СПЗ «Сланцы».
Анализируя
полученные данные, можно отметить повышенное содержание железа в смеси коксов с
ИркАЗа по сравнению с установленными требованиями, что может быть связано с
загрязнением коксов при шихтовке, перевалке и хранении на заводском складе.
Нефтяные
коксы отличаются более высоким содержанием серы и ванадия. Особенно это
касается кокса Пермского НПЗ. По содержанию золы все коксы вполне укладываются
в требования ТУ 1913-00200992-95. Выделяется только кокс с СПЗ «Сланцы», содержащий золу на верхнем допустимом пределе. Таким образом, с точки зрения
химической чистоты пековые коксы не уступают нефтяным, а кокс производства ЮАР
даже превосходит их.
При
выборе кокса-наполнителя для производства обожженных анодов, жесткие требования
предъявляются не только к химической чистоте. Сырье и технология должны
обеспечить, с одной стороны, получение анодов с высокой плотностью и низкими
пористостью и реакционной способностью при электролизе, с другой — достаточно
высокую механическую прочность и электропроводность анодов.
Поэтому
на втором этапе были исследованы объемно-структурные и электромеханические
характеристики коксов. Для стабилизации свойств все коксы (кроме прокаленного
пекового кокса производства ЮАР и прокаленного нефтяного кокса СПЗ «Сланцы»)
прокаливали при температурах 1100—1220 °С: нефтяные коксы — до действительной
плотности (а?Дейст) 2,02, 2,05, 2,07 г/см3; смесь пековых коксов с ИркАЗа — до
1,98, 2,00, 2,02 г/см3. Полученные результаты представлены на рис. 1. На
графиках не приведены характеристики по коксу ЮАР, но все показатели по этому
коксу превосходят аналогичные для смеси коксов с ИркАЗа.
У
всех коксов с повышением температуры прокаливания отмечено закономерное
повышение объемной плотности и насыпного веса. Также было ожидаемым уменьшение
величины удельного электросопротивления с ростом температуры их обработки.
Обращает на себя внимание более высокая прочность пековых коксов.
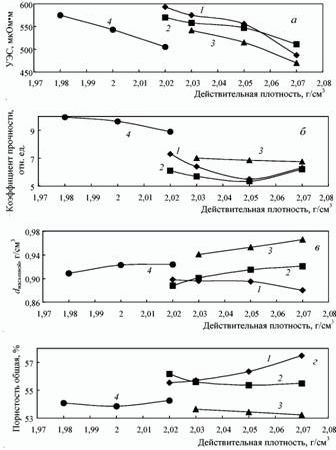
Рис.
1. Зависимость свойств кокса от действительной плотности:
а
— удельное электросопротивления (УЭС), мкОм • м; б — коэффициент прочности, отн. ед; в — насыпной вес, г/см3; г — общая пористость, %; 1 —кокс Пермского
НПЗ, 2 — кокс Ангарского НПЗ, 3 — кокс СПЗ «Сланцы», 4 — кокс ИркАЗ
На
основании результатов исследований можно сделать вывод, что пековые коксы имеют
более плотную структуру и превосходят нефтяные по показателям объемного и
насыпного весов и прочности при близких значениях электропроводности.
Также
можно отметить специфичные свойства нефтяного кокса, прокаленного на СПЗ
«Сланцы», который при одинаковой с нефтяными коксами действительной плотности
имеет похожие с пековыми коксами объемно-структурные характеристики. Вероятно, это объясняется свойствами коксов, которые шихтуются перед прокаливанием, и
особенностями технологии процесса прокалки кокса в ретортных печах.
Для
технологии производства обожженных анодов, как и для других видов прессованной
углеродной продукции, очень важным является правильный подбор упругих и
пластических свойств кокса-наполнителя. Данные свойства характеризуются
коэффициентом упругого расширения (Кур) и коэффициентом релаксации (Крел).
Методика и устройство для определения коэффициентов разработана А. Ф.
Красюковым [3].
Известно, что чем выше способность материала к релаксации (пластичность), тем он лучше
уплотняется без разрушения частиц при наложении давления. В то же время, чем
больше упругое расширение кокса, тем в большей степени спрессованный материал
стремится вернуться в исходное состояние после снятия нагрузки. Понятно, что с
повышением Кур кокса увеличивается вероятность расслоения образца и образования
трещин.
Учитывая
разнонаправленность изменения Крел и Кур при наложении давления прессования, А.Ф. Красюков ввел понятие коэффициента прессовой добротности (Адц), характеризующего преобладание пластических свойств над упругими.
На
третьем этапе, используя указанный подход к оценке технологических свойств
наполнителей, проводили изучение прессовых характеристик прокаленных коксов
(фракция 1,0—1,5 мм) в интервале давления прессования 200—800 кг/см2. При
увеличении поверхности шлифов коксов в 1000 раз также изучалась их структура.
В
интервале давления от 200 до 600 кг/см2 (см. рис. 2) происходит значительное
снижение Кпд на основании чего можно сделать вывод, что в данном интервале
давление прессования может влиять на физические свойства «зеленых» и обожженных
образцов. При более высоком давлении от 600 до 800 кг/см2 зависимости
становятся более монотонными и значения отличаются друг от друга незначительно.
В указанном интервале начинает происходить раздавливание материала, вследствие
этого нарушается начальный фракционный состав шихты и возникают предпосылки к
возникновению трещин в «зеленых» образцах за счет сил упругого расширения после
окончания прессования.
Рекомендуем скачать другие рефераты по теме: диплом государственного образца, рефераты помощь.
Предыдущая страница реферата |
1
2
3
4
5
6
7
8
9
10
11 |
Следующая страница реферата